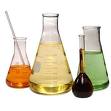
Pretreat- ment
We use a 5 stage pretreatment system. Other coaters may use the 3-stage system but we feel the 5 stage system gives our customers the best preparation for powder coating new materials. The 5 stage system provides superior pretreatment for powder coating final quality, appearance, and performance.
The 5 stage preparation system starts by first cleaning clean your work at an elevated temperature, assuring we remove dirt and grease that maybe remaining on the piece from manufacturing and handling. Then the item is rinsed in stage 2, making sure no cleaning chemicals are left before stage 3. In stage 3 we treat the piece with a phosphate solution that creates an adherent coating, paving the way for a supper stick surface for powder coating. Stage 4 is another rinse in which any extra phosphate is removed. The last stage seal rinses the piece against rust. It also helps to extend salt spray performance. The stage solutions are replaced after each batch so that fresh solutions are available for your part.
In combination, we use a heated spray wand dispersal system, delivering ample heat, that handles hard to clean work pieces and easily handles bulky or odd shaped pieces. This allows us to review every inch of your part and make sure the preparation is right and ready for coating.
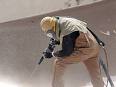
Sand Blasting
Sand blasting is a great way to remove old paint and rust from parts prior to powder coating. It not only removes surface contaminates but also gives the metal a fine texture that allows the powder coating to adhere to the metal for even better strength.
If you have your parts sand blasted before sending them to us please clean any oil and grease off before blasting. This will produce the best finish (oil and grease can be pushed into the surface and cause adhesion problems.
For Customers that have parts with paint or rust still on the parts, we offer a sand blasting service at a nominal hourly charge. Feel free to either E-mail, or call with any questions you have regarding sand blasting.
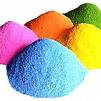
Color Charts
We carry many different brands, textures, and finishes to meet our customer´s every need.
Dupont Coating Solutions
Sherwin Williams Powdura
Tiger Drylac
Cardinal Industrial Finishes
Prismatic Powders (NIC Industries)
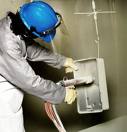
Powder Coating
Powder coating is a completely dry finishing process used on a wide range of materials and products. Finely ground particles of pigment and resin are electro-statically charged and sprayed on to products to be coated. The parts are electrically ground so the charged particles adhere to them until melted and fused into a solid coating in an oven.
Any industrial product benefits from the advantages of powder coating: improved appearance, exceptional toughness and durability, scratch-resistant, high quality, colorful, versatile, and long lasting. In addition to a wide range of colors and textures, and almost infinite range of properties can be built into the finish. Examples include resistance of ultra-violet rays, enhanced durability, and better corrosion resistance. Unlike liquid paint, no solvents are used, so only minimal amounts of VOC´s, if any, are released into the air. The powder coating process is environmentally friendly and virtually pollution-free.
Thousands of different kinds of parts and products are now powder coated. Examples include dryer drums, refrigerator liners, hospital beds, metal furniture, electrical cabinets, lighting fixtures, power saws, farm implements, curtain rods, ceiling fans, light truck bodies, small under hood parts, bicycle frames, and tackle boxes.